Segador
Una cosechadora (también en inglés: cosechadora ) es una máquina cosechadora agrícola para segar , trillar el grano o las semillas, separar la paja y el grano o las semillas , limpiar los granos y las semillas del vertedero y depositar la paja en hileras para su posterior recuperación como hojarasca o distribución plana de la paja picada para la fertilización natural en el campo.

1) carrete 2) barra de corte 3 ) sinfín de entrada 4) transportador inclinado 5) trampa de piedras 6) tambor de trilla 7) cóncavo de trilla | 8) Agitador de bandejas 9) Piso escalonado 10) Soplador 11 ) Tamiz superior 12 ) Tamiz inferior 13) Retorna el sinfín 14) Retorna | 15) Sinfín de grano 16) Tanque de grano 17) Picador de paja 18) Cabina del conductor 19) Motor 20) Sinfín de descarga 21) Tambor giratorio |
Descripción de los ensamblajes
Encabezamiento
En la parte delantera de la cosechadora está el encabezado. Dependiendo del tipo de cultivos trillados , se utilizan diferentes unidades. Si el cabezal es más ancho de tres metros (son posibles anchos de trabajo de casi 15 metros para el grano y 12 metros para el maíz), el cabezal debe desmontarse o plegarse (hidráulicamente) para viajar por carretera. A continuación, la unidad de corte se transporta con un carro de unidad de corte.
Unidad de corte desmontada sobre carro de transporte. Separadores de tallos plegados a los lados. En la barra de corte están montados Grainlifter (aquí: ángulo triangular rojo o metálico) para levantar el grano almacenado .
Unidades de corte
Una unidad de corte consta de la mesa de corte y los divisores de tallos, que dividen los tallos de grano de la pista a segar del resto del grano, si es necesario, orejeras, que se supone que se mueven debajo y erigen los tallos de grano acostados (grano almacenado), el carrete que alimenta los tallos de grano a la segadora de barras, la segadora manual y el sinfín de entrada o la cinta transportadora, que alimentan los recortes al mecanismo de trilla.
Cabecera de colza
Al cosechar colza , se colocan cuchillas de corte de tijera a los lados de la unidad de corte para separar las trayectorias de corte y la mesa de corte se alarga. La colza se cae de las cabezas de las semillas con mucha facilidad y las plantas individuales ramificadas se enredan entre sí. Destrozar las plantas de colza enredadas provocaría pérdidas considerables de grano. La extensión atrapa las semillas que son derribadas por el carrete. → Separador de colza
Cabezales de maíz
Los recolectores de maíz o los cabezales de maíz están diseñados de tal manera que los tallos de las plantas se tiran a través de un espacio estrecho a medida que pasan. El ancho del espacio del cortador de maíz debe corresponder lo más exactamente posible al diámetro del tallo de maíz. Dependiendo del sistema, el ancho del espacio se establece manualmente desde la cabina del conductor o automáticamente por la unidad de hilera respectiva. Si el ancho del espacio se establece correctamente, solo la planta de maíz se extrae a través del espacio, mientras que la mazorca de maíz más ancha se separa de la planta. Este permanece por encima de la unidad de corte y luego se alimenta al transportador inclinado de la cosechadora con la ayuda de las cadenas transportadoras y el transportador de tornillo sin fin. Al mismo tiempo, un picador colocado debajo de la mesa corta las plantas restantes. Para el grano también existen decapantes de maíz o simplemente llamados decapantes. Trabajan según el mismo principio que los recolectores de maíz. La ventaja es que la paja no tiene que pasar por la máquina, lo que aumenta la producción horaria de la cosechadora.
Cabeceras de girasol
Al trillar girasoles, las inflorescencias se separan del tallo. En términos de estructura, los cabezales de girasol son similares a los de maíz.
Recoger
En existencias de maduración desigual, la fruta se corta primero con una hileradora y se coloca en una hilera. Una vez que la fruta ha madurado más en la hilera, la cosechadora la recoge con un recolector para trillar.
Transportador inclinado
El transportador inclinado, también conocido como rampa, transporta el cultivo a la máquina. En el interior corre una cadena de alimentación que toma la cosecha del sinfín y la alimenta a la unidad de trilla.
Trampa de piedra
Hay una trampa de piedras inmediatamente al final del transportador inclinado. Se supone que el tambor de trilla empuja las piedras más pesadas allí. Dado que las cosechadoras rotativas son particularmente sensibles a las piedras que se tiran, existen sistemas en los que las piedras son reconocidas por sensores de golpe y, cuando se detectan piedras, la parte inferior del elevador se abre para que la piedra pueda volver al suelo.
Mango giratorio
El órgano de trilla consiste en un cóncavo en el que un tambor de trilla o un rotor gira a alta velocidad. El espacio entre el tambor / rotor y la canasta es muy estrecho. El grano se quita de la paja y cae a través de la malla de la canasta. Aproximadamente el 90% de los granos son separados por el Dreschaggregat de la paja y van directamente a la limpieza , solo la paja y el grano residual que aún contenía llegan a la deposición . Dependiendo del tipo de fruta a trillar, la intensidad de la trilla se puede variar variando la velocidad del tambor y cambiando el espacio de trilla entre el tambor de trilla y el cóncavo.
Se puede lograr una trilla aún más intensa cerrando las primeras filas de jaulas o instalando barras de fricción. Esto es necesario si se van a romper las aristas de los granos de cebada o si se trilla la fruta donde las semillas están muy firmemente adheridas a las inflorescencias. Se reduce el área de separación de la cesta.
Declaración
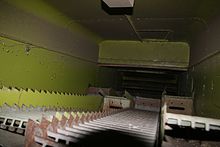
El cultivo se separa de la unidad de trilla, donde se separan de la paja el resto de granos y espigas que no han sido completamente trilladas. Existen diferentes sistemas de separación:
El sistema de separación clásico es el llamado agitador de bandejas (ver imagen a la derecha). Consiste en varias ranuras en forma de diente de sierra de aproximadamente 20 cm de ancho unidas a un cigüeñal , a través de las cuales el material se mueve hacia atrás debido al movimiento de agitación, por lo que la paja más liviana y mucho más grande sigue a los agitadores ascendentes. Los granos y las mazorcas que no se han trillado completamente se separan de la pajita y caen a través de pequeños orificios en las bandejas hacia los bolsillos de la coctelera y se deslizan sobre el tamiz de limpieza.
Otro sistema de separación es el sistema axial . La separación se realiza con uno o dos rotores instalados longitudinalmente ( axialmente ), cuya funcionalidad es similar a la de un separador . Una jaula (similar a una cóncava) se coloca debajo de los rotores, que guía la paja hasta que llega a la parte trasera de la cosechadora o picadora .
limpieza
Los elementos a limpiar, que consisten en granos y NKB (componentes no granos = partes de paja y paja), se limpian mediante el mecanismo de trilla y otros elementos de separación (agitadores o rotores de separación). Esta mezcla se suele limpiar mediante dos tamices dispuestos uno encima del otro , los tamices superior e inferior . Los
elementos a limpiar se alimentan a los tamices de diferentes formas , según el fabricante: a) A través de un piso escalonado (chapa perfilada escalonada), que se encarga tanto del transporte como de la distribución uniforme en las direcciones longitudinal y transversal y de una determinada grado de segregación previa. b) A través de un transporte activo mediante varios tornillos adyacentes , cuya función principal es ganar altura dentro del proceso de limpieza y alimentar los elementos a limpiar de manera uniforme a los tamices. c) Uno o más, con ayuda de un ventilador, peldaños de caída ventilados, que expulsan una gran proporción de las fracciones ligeras de paja de los artículos a limpiar antes de que lleguen a los tamices. Sobre todo, esto asegura que los granos golpeen la superficie de la pantalla debajo del NKB y se separen rápidamente.
Ambas pantallas están ventiladas desde abajo mediante una corriente de aire (viento). Esto asegura que los artículos que se van a limpiar se aflojen y, en el mejor de los casos, se crea la denominada fase de lecho fluidizado. Los componentes ligeros, como la paja y la paja corta, "flotan" y permiten que los granos mucho más pesados lleguen a la superficie del tamiz.
Los artículos a limpiar primero pasan del alimentador al tamiz superior. Esto tiene esencialmente la función de separar los granos y las mazorcas no arrojadas (relaves) al tamiz inferior y transportar el NKB fuera de la cosechadora a través del extremo del tamiz. El tamiz inferior representa la última etapa de limpieza, en la que, en el caso ideal, se logra una pureza de grano superior al 99,6%. El grano puro se transporta mediante un tornillo a un lado de la máquina (generalmente a la derecha en el sentido de la marcha) y desde allí mediante un elevador al depósito de grano. La transición del tamiz del tamiz inferior (relaves) consiste en mazorcas sin trillar, granos y paja. Estos retornos se transportan a uno o ambos lados de la cosechadora con un tornillo y desde allí se devuelven a la unidad de trilla o los elementos transportadores para su limpieza con la ayuda de otro tornillo o un elevador. Los fabricantes que devuelven las devoluciones para su limpieza instalan un pequeño dispositivo de trilla adicional en el camino.
Dado que de la cosechadora salen grandes cantidades de semillas de malas hierbas con el NKB, la paja y la paja (si se cortan ) se distribuyen en todo el ancho de trabajo en la medida de lo posible con anchos de corte de más de 3 metros, por ejemplo mediante un disco esparcidor de paja con forma. La limpieza se puede ajustar al tipo de grano a trillar cambiando los diseños de tamiz superior e inferior y variando la velocidad del viento. Tanto la frecuencia como la amplitud de la oscilación del tamiz suelen ser especificadas por el fabricante y solo pueden cambiarse con una gran remodelación .
Manejo de granos y paja
El depósito de grano sirve como contenedor de almacenamiento del grano y tiene una capacidad de entre 5 y 18 metros cúbicos, según el tamaño de la cosechadora. Por lo general, está dimensionado para que el grano se pueda trillar durante 15-30 minutos sin vaciar el tanque. Luego, el grano se descarga , a menudo en paralelo a la trilla, a través de la tubería de descarga en un remolque de transporte o un vehículo de transferencia . Máquinas potentes como la AGCO Ideal 9 PL pueden gestionar hasta 210 l / s. Esto significa que el depósito de grano completamente lleno se puede vaciar en menos de 100 segundos.
En la parte trasera de la cosechadora, detrás de los elementos de trilla y separación, la paja trillada se expulsa de la cosechadora. La paja puede ser colocada o cortada para su posterior recuperación con una empacadora en hilera . Para la colocación de hileras, las cosechadoras suelen tener placas de guía o púas con las que se puede ajustar el ancho de la hilera para adaptarla a la empacadora. A menudo se instala un picador de paja en las máquinas más nuevas , que corta la paja trillada en trozos pequeños y la distribuye por todo el ancho de corte. La paja picada se puede trabajar más tarde en el suelo y, por lo tanto, ayuda a aumentar el contenido de humus . Con anchos de corte cada vez mayores, la distribución uniforme de la paja es un desafío importante para los fabricantes de hoy.
motor
Con una potencia nominal de 581 kilovatios (790 CV ), la Claas Lexion 8900 es actualmente la cosechadora con mayor potencia de motor. Las cosechadoras combinadas modernas necesitan la potencia sobre todo para la unidad de trilla, los elementos de separación y el picador de paja. Dependiendo de las condiciones de cosecha y del ancho de trabajo, la picadora por sí sola consume hasta un 20% de la potencia disponible. Dado que se genera mucho polvo durante la trilla, el suministro de aire de combustión y refrigeración al motor es problemático. Por lo tanto, el filtro de aire y el enfriador deben mantenerse limpios mediante un equipo mecánico, que se realiza mediante succión, cepillos giratorios o un engranaje de inversión del ventilador. El engranaje de marcha atrás cambia la dirección de rotación del ventilador del radiador brevemente a partir de una cierta temperatura para que sople el radiador.
tren de aterrizaje

Toda la máquina se asienta sobre un chasis dominado por dos ruedas grandes y anchas (a menudo de más de 80 cm de ancho) directamente detrás de la unidad de corte y debajo de la cabina. Las ruedas traseras más pequeñas se utilizan para la dirección. Cuando se utiliza en terrenos difíciles, se utilizan tracción total y cada vez más orugas , cuyas ventajas son, por un lado, una menor compactación del suelo y, por otro lado, el funcionamiento más suave de la máquina, lo que es particularmente importante con Unidades de corte muy anchas. Al diseñar una cosechadora como manillar trasero, se puede lograr un círculo de giro muy estrecho con la unidad de corte montada directamente en la parte delantera del eje delantero.
Dado que la velocidad de conducción óptima depende de muchos factores durante la trilla (potencia del motor, Dreschverluste, densidad de población , grano almacenado , terreno irregular, etc.), es importante que la velocidad de la cosechadora se pueda variar continuamente. Esto generalmente se hace mediante transmisiones hidrostáticas o de variador .
Cabina del conductor
En lugar del asiento del conductor abierto, que era común en las primeras cosechadoras combinadas, directamente detrás de la unidad de corte y sobre el transportador inclinado con mucho polvo, ruido y, si el clima lo permite, exposición al calor para el operador de la máquina, se recomienda una cabina del conductor cerrada. casi sin excepción construida en el mismo lugar en modernas cosechadoras. Esto permite una protección eficaz del conductor contra el polvo, el ruido y el calor y, por lo tanto, suele estar climatizado y diseñado cómodamente para una larga jornada de trabajo (normalmente entre 10 y 14 horas). También contiene los controles electrónicos y pantallas para configurar y monitorear todos los parámetros relevantes de la cosechadora (pantallas del motor, control de la unidad de corte y la unidad de trilla, cada vez más instrumentos para medir el rendimiento, a veces combinados con sistemas de registro GPS ).
El control de la unidad de corte, el tubo de descarga y la velocidad de conducción se realiza con una palanca, que se sostiene constantemente en la mano derecha del conductor (la mano izquierda está en el pomo del volante). En las cosechadoras modernas, este es un joystick que controla la electrónica. En los modelos más antiguos, una palanca está conectada mecánicamente a las unidades de control hidráulico. La función de la unidad de control (altura de la unidad de corte, distancia desde el carrete / mesa de la unidad de corte, velocidad de conducción) se selecciona seleccionando la compuerta de palanca. Se pueden proporcionar más carriles de palanca, por ejemplo, para la velocidad del molinete o del tambor de trilla, pero normalmente solo son accesibles después de soltar un dispositivo de seguridad para evitar un ajuste involuntario.
automatización
En los últimos años, cada vez más tareas de control y seguimiento que antes realizaba el conductor han sido asumidas por dispositivos automatizados. Por ejemplo, la unidad de corte sigue automáticamente el terreno irregular a una altura de corte especificada por el conductor. Los sensores detectan el terreno irregular y, a continuación, el control automático cambia la altura de trabajo y la inclinación de la unidad de corte de acuerdo con los datos del sensor. Otro paso en la automatización son los sistemas de dirección automática. Mediante DGPS , se puede determinar la posición de la cosechadora en el campo con una precisión de ± 10 cm. Con esta información, la computadora de a bordo guía la cosechadora a lo largo del carril anterior a través del campo. El conductor solo necesita tomar el volante en sus manos al final del campo para hacer girar la máquina. También existen sistemas que utilizan sensores para medir la cantidad de cosecha y ajustar la velocidad de la cosechadora para que siempre conduzca con la capacidad óptima.
historia
Hasta la mecanización de la agricultura , el grano se cosechaba a mano en varios pasos , si se ignora la segadora galorromana ( vallus ), que desapareció con el fin de la antigüedad . Primero, el grano se cortaba con una hoz , un tamiz o una guadaña y, por lo general, se ataba en gavillas que inicialmente permanecían en el campo. La siega se llevó a cabo antes de que se necesitara el grano para que la cosecha estuviera muerta; El cultivo cosechado, que se colocó en gavillas en el campo, maduró y se secó para que ni el grano ni la paja tuvieran la sequedad necesaria para el almacenamiento final al momento de la siega. Como regla general, las gavillas se transportaban a la granja para trillar el grano, a menudo después de un almacenamiento adicional, en el granero en el piso de trilla con mayales . Luego se limpió de la paja e impurezas como la tierra o las semillas de malezas mediante un tamizado o aventado . Al aventar, los componentes ligeros de la trilla arrojados fueron arrastrados como paja por el viento. Posteriormente, se utilizaron para esto simples barredoras de viento manuales , en las que una caja de tamiz dejaba que el grano se filtrara a una caja de viento que se adjuntaba debajo; esta separación de aire sigue siendo parte de la etapa de limpieza de las cosechadoras hoy en día.
Con el inicio de la mecanización, las trilladoras estacionarias se desarrollaron inicialmente alrededor de 1786 , que inicialmente eran accionadas a mano o por animales a través de gopels . Las máquinas de vapor, motores de combustión interna , motores eléctricos y otras unidades fueron posteriormente utilizados. La primera segadora para cereales fue desarrollada en 1826 por el clérigo escocés, el reverendo Patrick Bell. Con la invención del anudador mecánico en 1857, fue posible construir aglutinantes para segadoras que ataban el grano en poleas de una manera totalmente mecanizada. Inicialmente, estas máquinas eran tiradas por caballos e impulsadas por las ruedas de la máquina. Con la aparición de tractores útiles, inicialmente se utilizaron en lugar de caballos para entrenar. En 1927, Krupp produjo su primera cortadora de césped, impulsada directamente por el motor del tractor a través de un eje de toma de fuerza .
Las cosechadoras combinadas, que también son móviles, son el resultado de la combinación de una segadora y una trilladora móvil. Ya en 1834, Hiram Moore y James Hascall demostraron una máquina en Michigan que podía segar y trillar además de limpiar; el ancho de trabajo fue de 4,60 metros. La máquina fue patentada en 1836. Se necesitaban hasta 40 mulas o caballos para tirar de estas máquinas. Los órganos de trilla y limpieza eran accionados por una de las ruedas. George Stockton Berry construyó la primera cosechadora autopropulsada con motor de vapor en 1886. La caldera se quemó con la paja trillada y también suministró vapor al accionamiento separado de los órganos de trilla. En 1911, la Holt Manufacturing Company de Stockton, California utilizó por primera vez motores de combustión interna en cosechadoras; sin embargo, solo manejaban el sistema de trilla, separación y limpieza y no el chasis.
La primera cosechadora autopropulsada de un fabricante alemán fue la MD 1 de Maschinenfabrik Fahr ; se presentó a la agricultura por primera vez en la exposición DLG en Hamburgo en 1951. A principios de la década de 1950, las cosechadoras combinadas arrastradas seguían desempeñando un papel importante en Alemania. Las cosechadoras exitosas como la Lanz MD 50, la IHC D61 y la MF 30 se vendieron por alrededor de 10.000 marcos alemanes. Durante el auge de los tractores, a veces había 12 fabricantes de cosechadoras en Alemania, pero no todos pudieron establecerse en el mercado. La cosechadora se estableció como una máquina cosechadora a partir de la década de 1970. New Holland lanzó una primera cosechadora rotativa en 1975.
Cosecha de cereales con Stalinez 4 (1953)
Combinar tipos
Las cosechadoras se diferencian según el tipo de locomoción y la forma en que funcionan.
unidad de tracción
Según el tipo de locomoción, se distingue entre vehículos autopropulsados y dispositivos tirados por animales de tiro o tractores . En el caso de las máquinas remolcadas, existen dispositivos que impulsan los elementos de corte y trilla a través del eje de la TDF del tractor, así como los que son impulsados por un motor de combustión interna separado (motor auxiliar); el tractor o los animales de tiro solo tienen el dispositivo sobre el campo para mover.
Funcionamiento de órganos de trilla y separación.
Según la forma de trabajar, existen tres categorías:
- Cosechadora convencional con tambor de trilla y sacudidor de cremallera, ver diagrama anterior
- Cosechadora axial sin tambor de trilla: solo los rotores realizan la trilla y la separación
- Cosechadora híbrida con tambor de trilla y rotor
El sistema de trilla actual consta de un tambor de trilla y un cóncavo. Aquí se hace una distinción entre cuatro conceptos básicos.
Sistema de trilla tangencial (convencional)
El eje del tambor de trilla es perpendicular a la dirección de desplazamiento en la cosechadora. Por tanto, el flujo del cultivo es tangencial al tambor. Dependiendo de los requisitos de rendimiento, se instalan dos o más unidades giratorias. Las unidades tangenciales nunca se envuelven en la pajita durante más de tres cuartos de vuelta. Luego, la paja trillada vuelve a salir del tambor. No todos los granos caen por el cóncavo en este corto camino. Entonces se necesita otro sistema de separación.
Sistema de trilla axial
En el caso de las unidades de trilla axiales , el eje de rotación del rotor corre en el sentido de la marcha. La pajita se guía varias veces alrededor del rotor. Las placas inclinadas en el interior superior del tambor del rotor provocan el empuje hacia atrás. Por lo tanto, la dirección de flujo principal del cultivo es a lo largo del eje.
La trilla se realiza en la sección delantera del rotor, la separación en la sección trasera. Debe encontrarse un compromiso entre la velocidad de trilla y la velocidad de separación. John Deere trabaja aquí con diferentes diámetros de rotor / carcasa en el flujo de cultivo. Un fabricante ruso utiliza cestas giratorias. La eficiencia de separación de los rotores es muy alta. Las pérdidas no aumentan tanto como aumenta el rendimiento como lo hacen con la separación del agitador.
Debido al método de construcción mucho más simple y la ventaja de costos resultante, este método de construcción se ha establecido en América del Norte y del Sur, así como en Rusia. Con las condiciones de trilla favorables que prevalecen allí, se pueden lograr rendimientos que son solo insignificantemente inferiores a los de los sistemas híbridos y significativamente superiores a los de los sistemas tangenciales.
La paja está sujeta a una gran tensión mecánica y, por lo tanto, casi no se puede procesar más como paja larga.
Sistema de trilla transversal
Funcionalmente, el sistema de trilla transversal es similar al sistema de trilla axial. También se utiliza un rotor para trillar y separar. Sin embargo, el eje de rotación se encuentra transversalmente en la cosechadora. Esto significa que el material a trillar no tiene que ser desviado en su flujo natural, como ocurre cuando se alimenta un rotor axial. A diferencia del tambor de trilla, la cosecha se lleva más de una vuelta completa en el rotor. El sistema de trilla transversal se instala principalmente en pequeñas cosechadoras especializadas para la trilla de arroz (por ejemplo, Claas Crop Tiger). Para las cosechadoras convencionales, el sistema solo lo ofrece AGCO-Gleaner.
Sistemas de trilla híbridos
En el sistema de trilla híbrido, el cultivo se trilla en uno o más tambores de trilla tangenciales y luego se alimenta a uno o más rotores separadores. La ventaja del rotor separador sobre el agitador es que permite una separación mucho más intensa de la paja y la paja. La desventaja es que la pajita está más estresada y la pajilla rota ejerce una mayor presión sobre la limpieza. Por lo tanto, la limpieza es el factor limitante en muchos modelos. Por esta razón, la velocidad de los rotores del separador debe adaptarse a las condiciones de cosecha para encontrar un compromiso entre la separación y el rendimiento de limpieza.
Sistemas de separacion
Cuando se trata de separación, se hace una distinción entre dos tipos de órganos de separación fundamentalmente diferentes.
- Agitador de bandejas: En las cosechadoras convencionales, la separación se realiza mediante un agitador de bandejas. El agitador consta de cuatro a seis bandejas con puntas en forma de púa unidas a la parte superior. Todas las bandejas están unidas a dos cigüeñales que giran. El resultado es un movimiento circular excéntrico de la bandeja: primero hacia arriba, luego hacia atrás, luego hacia abajo y luego hacia adelante. Cuando una horda está en la cima, las hordas a su lado son más profundas. En el camino hacia arriba, las hordas se apoderan de la estera de paja de la que está al lado y la llevan a la parte trasera con las púas. A medida que se mueven hacia abajo, devuelven el tapete a las bandejas contiguas. Vacíos corren de nuevo hacia adelante en el sentido de la marcha.
- Como resultado, la paja se lanza de tal manera que los granos que aún se transportan caen a través de la estera de paja. Debajo de cada estante hay una tina en la que los granos corren en diagonal hacia el piso de preparación.
- La coctelera es el sistema de separación que menos esfuerzo ejerce y destruye la pajita. La eficiencia de separación disminuye rápidamente con paja húmeda o inmadura. Al conducir cuesta arriba, las pérdidas también aumentan porque la inclinación de la pendiente se opone a la tendencia a temblar. En la pendiente lateral, la bandeja limita la capacidad de separación en la parte inferior de la pendiente. En estas condiciones, la velocidad de conducción debe reducirse.
- Elementos de separación axiales: las cosechadoras con unidades de corte muy anchas se construyen por lo tanto con elementos de separación axiales. Uno o dos rotores axiales (luego dispuestos uno al lado del otro) asumen la tarea de separación. Las fuerzas centrífugas separan el grano y la paja entre sí. Los elementos formados por una estructura de cesta que rodean el rotor al menos por debajo evitan que demasiados componentes no granulares lleguen al sistema de limpieza y, por lo tanto, restringen su funcionalidad. Con los sistemas axiales, la pajilla atraviesa la separación unas diez veces más rápido que con los sistemas de agitación. Por lo tanto, son posibles rendimientos más altos y la pérdida de grano es significativamente menor, especialmente en condiciones de cosecha húmedas. Las cosechadoras combinadas axiales también son menos susceptibles a pendientes pronunciadas, ya que la gravedad es menos importante para la separación.
Cosechadora de pendientes
Como regla general, el grano se cultiva en superficies planas. Sin embargo, hay regiones donde los cultivos de trilla se cultivan en topografías de suaves colinas y, a veces, bastante empinadas. Como se describió anteriormente, el proceso de trilla y separación en cosechadoras combinadas está muy influenciado por la topografía o la fuerza de la gravedad. El hecho de que la unidad de trilla se alimente por un lado debido a la inclinación de la pendiente reduce enormemente el rendimiento de la máquina, ya que no se utiliza todo el ancho de la unidad de trilla. Sin embargo, lo peor es la carga unilateral del sistema de limpieza (piso de preparación, tamices) con los productos trillados. La paja y el grano llegan al sistema de limpieza en el lado de la pendiente y el movimiento del tamiz concentra aún más el material en un lado.
La penalización por rendimiento aumenta exponencialmente con la pendiente. Por eso es de gran interés la pendiente respectivamente. para compensar esta degradación del rendimiento. Existen varios sistemas para esto.
Chasis inclinado
El método más antiguo que todavía se utiliza hoy en día, especialmente en pendientes extremas, es que el chasis se eleva o se baja para que los elementos de trilla queden horizontales. La primera cosechadora con compensación de pendiente basada en este principio fue construida en 1891 por los hermanos Holt en California. La compensación de pendiente tenía que establecerse mecánicamente en máquinas anteriores, lo que requería una segunda persona en la cosechadora. La primera compensación automática de pendiente fue desarrollada por Raymond A. Hanson en 1941. En 1945 equipó las primeras máquinas con este sistema, en el que se determinaba el grado de inclinación mediante un interruptor de mercurio y los elementos separadores se alineaban en consecuencia mediante cilindros neumáticos.
Hoy en día, la compensación se realiza habitualmente mediante dos cilindros hidráulicos que levantan la cosechadora por un lado del eje delantero y así la sujetan horizontalmente. Dado que el eje trasero gira, no se requiere compensación de inclinación. En raras ocasiones, el sistema hidráulico de elevación del eje trasero también permite compensar la inclinación en la dirección longitudinal.
El esfuerzo técnico y los costos asociados son problemáticos aquí. La transferencia de cultivos de la barra de corte inclinada a la cosechadora recta también es problemática. Sin embargo, este sistema tiene la ventaja de que todo el vehículo, a excepción de la unidad de corte, se mantiene en posición horizontal. Por lo tanto, el rendimiento de los órganos de limpieza no se ve afectado por acostarse de lado. El volumen del depósito de grano también se puede aprovechar al máximo, lo que no es posible si el vehículo se inclina hacia un lado, ya que la cosecha se deslizaría hacia este lado, lo que en casos extremos puede incluso provocar el vuelco del vehículo. Además, aumenta la comodidad de conducción, ya que el conductor también permanece en una posición sentada recta y no amenaza con deslizarse fuera del asiento.
Láminas transversales
Como otro sistema muy simple, las placas transversales se han establecido en los tamices, que solo permiten que la mercancía se deslice hacia el lado de la pendiente de manera limitada.
Compensación de pendiente
Como solución adicional, Claas confía en la compensación de pendiente. Se mide la inclinación de la pendiente y las cribas se colocan en una oscilación transversal en función de la inclinación mediante un actuador hidráulico. Como resultado, el material se transporta cuesta arriba contra la gravedad y, por lo tanto, se distribuye uniformemente. New Holland también ofrece sistemas de compensación de pendiente que, dependiendo de la pendiente, que está determinada por un nivel de burbuja electrónico, mantienen todo el proceso de limpieza (caja de cribado y ventilador) en posición horizontal mediante un motor eléctrico de husillo. Ambos sistemas solo compensan las inclinaciones laterales de la máquina.
Cosechadora-trilladora rotativa
En las cosechadoras rotativas, las posiciones inclinadas en pendientes no tienen una influencia significativa en la separación del grano residual, ya que esta se realiza de forma rotativa en lugar de mediante agitadores que funcionan según la posición. Dado que la limpieza se realiza habitualmente de forma convencional como caja de cribas, las cosechadoras rotativas también se ofrecen con equilibrado manual.
Fabricante
La concentración empresarial que se ha producido en muchas áreas en los últimos años también se puede observar en el sector agrícola. En el caso de las cosechadoras combinadas, los altos requisitos tecnológicos y la producción intensiva en capital también contribuyen al hecho de que muchas empresas anteriormente independientes ahora están unidas en un grupo paraguas . Las marcas establecidas se conservan parcialmente unas junto a otras o, por ejemplo, a nivel regional o en la gama de productos, se diferencian. Si bien las marcas menos conocidas o respetadas se están abandonando, las empresas con una imagen de alta calidad pueden hacerse cargo de líneas de productos previamente inexistentes con sus propios nombres de empresas hermanas.
- John Deere es el líder mundial en maquinaria agrícola.
- Claas es el líder del mercado europeo de cosechadoras.
- En el grupo CNH Industrial , el segundo mayor fabricante de maquinaria agrícola del mundo, la marca GDR , entre otras cosas, fue progresando , las marcas de hoy son
- Case IH y
- New Holland .
- AGCO ( Allis-Gleaner Corporation ), formada en 1990, combinó varias marcas conocidas:
- Gleaner ha sido la marca de las cosechadoras desde el principio.
- Massey Ferguson fue adquirido en 1994.
- Fendt se unió al grupo en 1997 y ha estado vendiendo cosechadoras bajo su propio nombre desde 1999.
- Laverda es propiedad total del grupo desde 2010.
-
SDF vende cosechadoras bajo la marca:
- Deutz-Fahr es la empresa sucesora del primer fabricante alemán.
- Gomselmash es un fabricante bielorruso de, entre otras cosas, Cosechadoras combinadas.
- Rostselmasch es un fabricante ruso de, entre otras cosas, Cosechadoras combinadas.
- Sampo Rosenlew es un fabricante finlandés de, entre otros. Cosechadoras combinadas.
La empresa Zürn Harvesting , que la empresa Hege compró al inventor de este tipo de cosechadoras, Hans-Ulrich Hege , y Wintersteiger producen trilladoras de parcelas con fines de prueba .
Trivialidades
En el reverso de los billetes de 5 marcos (DDR) se representaba una cosechadora del tipo Progress E 512 .
literatura
- Udo Bols: cosechadoras en Alemania desde 1931 hasta la actualidad . 3 volúmenes, Podszun, Brilon 2005-2008, ISBN 978-3-86133-406-4 .
- Dr. Klaus Krombholz, el Dr. Hasso Bertram y Hermann Wandel: 100 años de ingeniería agrícola, desde la artesanía hasta la alta tecnología en Alemania . DLG-Verlag, Fráncfort del Meno, 2009, ISBN 978-3-7690-0737-4 .
- Graeme R. Quick, Wesley F. Buchele: Las cosechadoras de granos. Sociedad Estadounidense de Ingenieros Agrícolas, St. Joseph / Michigan 1978, ISBN 0-916150-13-5 .
- Manfred Baedecker, Ralf Lenge: La historia de la cosechadora Claas . Landwirtschaftsverlag, Hiltrup 2001, 2ª edición 2003. ISBN 3-7843-3053-3 .
enlaces web
- Representación animada de un sistema de separación de rotor
- Cómo funciona una cosechadora
- Informe de conducción a tiempo
Evidencia individual
- ^ Paul Schweigmann: Las máquinas agrícolas y su mantenimiento . Primera edición, Pfanneberg, Gießen 1955, reimpreso por Bulldog-Press, Limburg ad Lahn 1993, ISBN 3-9803332-1-3 , págs. 196-197
- ↑ Horst Eichhorn, Landtechnik, séptima edición, Ulmer, Stuttgart, 1952, 1999, ISBN 3-8001-1086-5 , p. 259 f.
- ↑ Estudio de cosecha. En: Dragotec. 5 de agosto de 2020, consultado el 7 de mayo de 2021 (alemán).
- ↑ Datos técnicos de Fendt Ideal . AGCO / Fendt , 2 de agosto de 2019
- ↑ Claas Lexion 8000 . Claas , 2 de agosto de 2019
- ↑ http://www.cornways.de/hi_combine.html
- ↑ Archivo de copia ( recuerdo de la original, del 29 de septiembre de 2008 en el Archivo de Internet ) Información: El archivo de enlace se inserta de forma automática y sin embargo no ha sido comprobado. Verifique el enlace original y de archivo de acuerdo con las instrucciones y luego elimine este aviso.
- ↑ Archivo de copia ( recuerdo de la original, del 29 de septiembre de 2008 en el Archivo de Internet ) Información: El archivo de enlace se inserta de forma automática y sin embargo no ha sido comprobado. Verifique el enlace original y de archivo de acuerdo con las instrucciones y luego elimine este aviso.
- ↑ M. Baedecker, R. Lenge, págs. 13 + 14
- ^ Paul Schweigmann, Las máquinas agrícolas y su mantenimiento, primera edición, Pfanneberg, Gießen, 1955, reimpreso por Bulldog-Press, Limburg ad Lahn, 1993, ISBN 3-9803332-1-3 , p. 280 y siguientes.
- ↑ Archivo de copia ( recuerdo de la original, del 29 de septiembre de 2008 en el Archivo de Internet ) Información: El archivo de enlace se inserta de forma automática y sin embargo no ha sido comprobado. Verifique el enlace original y de archivo de acuerdo con las instrucciones y luego elimine este aviso.
- ↑ Archivo de copia ( recuerdo de la original, del 29 de septiembre de 2008 en el Archivo de Internet ) Información: El archivo de enlace se inserta de forma automática y sin embargo no ha sido comprobado. Verifique el enlace original y de archivo de acuerdo con las instrucciones y luego elimine este aviso.
- ↑ www.zuern.de
- ^ La empresa Zürn se hace cargo de la producción de las trilladoras de paquetería Hege
- ↑ www.wintersteiger.com (la página ya no está disponible , buscar en archivos web ) Información: El enlace se marcó automáticamente como defectuoso. Verifique el enlace de acuerdo con las instrucciones y luego elimine este aviso.