Espuma
Las espumas son materiales sintéticos con estructura celular y baja densidad . Casi todos los plásticos son aptos para la formación de espuma . Las espumas se pueden comprimir, es decir, su volumen se puede reducir significativamente aplicando presión (ver compresibilidad ).
Clasificación
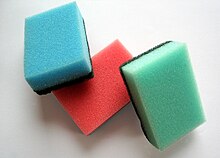
- Espuma de celda cerrada: las paredes entre las celdas individuales están completamente cerradas.
- Espuma de celda abierta: las paredes de las celdas no están cerradas, por lo que estas espumas pueden absorber líquidos .
- Las espumas de células mixtas contienen ambos tipos de células.
- Espumas integrales: Tienen una piel exterior gruesa y cerrada y un núcleo celular, la densidad disminuye hacia el interior.
- Ver también: Reticulante
propiedades
Las espumas se caracterizan por una densidad muy baja (aquí denominada peso volumétrico ) y una conductividad térmica con poca resistencia . El procesamiento y el mecanizado son fáciles con bajos costos de herramientas. Debido a la estructura interna, los componentes hechos de espuma están casi libres de tensiones internas .
Fuerza y peso
- La resistencia está en la dureza de compresión z. B. dureza de compresión 50 = 5.0 kPa al 40% de compresión (usualmente usada pero inexacta) o dureza de indentación (pero desconocida con significado) expresada. Por ejemplo, la resistencia a la compresión de 50 corresponde a aproximadamente 50 g / cm².
- El peso volumétrico se expresa en kg / m³, también viejos g / l.
La densidad z. B. RG 35 ≙ 35 kg / m³ y la dureza por compresión o indentación no dependen en su mayoría entre sí. La espuma pesada no tiene por qué ser rígida. Más bien, esto depende del uso de productos químicos crudos, el "clima" (el clima relativo durante la formación de espuma) y las habilidades técnicas del espumador. Esto da como resultado tolerancias . Se aceptan tolerancias de resistencia en el rango de ± 15% de un lote a otro y dentro del lote. La información sobre espumas z. Por ejemplo: RG35 / 50 = peso volumétrico / dureza de compresión (es decir, 35 kg / m³ / 5 kPa al 40% de compresión).
Proceso de formación de espuma
Diferenciación según el tipo de producción:
- Espuma física: el material se espuma mediante un proceso físico.
- Espuma química: se añade a los gránulos de plástico un agente de expansión, generalmente en forma de los llamados gránulos de mezcla maestra . Cuando se suministra calor, se separa un componente volátil del agente de expansión, lo que conduce a la formación de espuma de la masa fundida.
- Espuma mecánica: aquí se agita aire en la resina o pasta que se va a hacer espuma; esta espuma solidifica por reticulación de la resina o por gelificación de la pasta.
Extrusión de espuma
En la producción de espuma de PP-E (esto también es posible para polietileno , poliestireno , PET o algunos biopolímeros ), el polipropileno fundido se mezcla con gas propulsor (por ejemplo , pentano , CO 2 ) en la extrusora a alta presión . En el pasado, los CFC se usaban a menudo como propulsores , pero ahora su uso está prohibido en gran medida debido a sus efectos dañinos sobre la capa de ozono .
Al salir de una boquilla perforada, el plástico se expande de 20 a 50 veces su volumen. Las hebras de espuma resultantes se pueden acortar a partículas de espuma con un diámetro de aproximadamente 2-8 mm utilizando cuchillas giratorias en el granulador de anillo de agua o en el granulador submarino . Luego se separan del agua, se secan, se acondicionan en silos y luego se procesan en piezas de espuma moldeadas en el llamado proceso de moldeo.
Un proceso muy importante es la producción de láminas de espuma (por ejemplo, de PP o PE como aislamiento acústico de impacto ) o láminas de espuma (por ejemplo, XPS de poliestireno). En la mayoría de los casos, sin embargo, el proceso de extrusión continua se lleva a cabo con las denominadas extrusoras en cascada, es decir, dos extrusoras dispuestas una detrás de la otra. Mientras que el granulado de plástico se funde ("plastifica") en la primera extrusora, como ya se mencionó, después de que se haya añadido el agente de expansión en la segunda extrusora, este agente de expansión se mezcla muy uniformemente. Además, la masa fundida se lleva a un nivel de temperatura definido (generalmente un proceso de enfriamiento), después de lo cual se lleva al ancho aproximado de la película o placa posterior en una matriz de ranura. Debido a la presión ambiental más baja en relación con la presión de vapor del agente de expansión, la masa fundida se expande y se calibra al espesor de placa deseado en un dispositivo especial. Las siguientes unidades cortan los paneles al tamaño requerido o enrollan la película para que los productos estén disponibles para su posterior procesamiento.
Proceso de moldeo
El proceso de moldeo se utiliza para procesar partículas de espuma ( EPS , EPP , EPE ) en piezas de espuma moldeadas .
Se soplan perlas de espuma con un diámetro de aproximadamente 1–8 mm en moldes de aluminio poroso y se sinterizan juntas con vapor (aproximadamente 1,2 bar para EPS, aproximadamente 3 bar para EPP). Después de la fase de enfriamiento y estabilización, las piezas moldeadas recién creadas se pueden quitar del molde.
Este proceso de fabricación permite fabricar piezas de espuma termoplástica en el rango de densidad entre aproximadamente 12 kg / m³ y 300 kg / m³ con una distribución de densidad muy homogénea en toda la pieza de espuma. Los procesos de espumado directo con gases propulsores químicos o físicos en el moldeo por inyección no lo permiten debido a la velocidad de enfriamiento limitada con espesores de pared mayores.
El proceso de moldeo consume mucha energía , ya que la herramienta (molde) y las partes de la máquina de moldeo (cámara de vapor) deben calentarse y enfriarse nuevamente con cada ciclo (disparo) .
Las áreas de aplicación de las piezas moldeadas de EPP son z. B. contenedores aislados, aislamiento térmico, embalajes de transporte reutilizables y, cada vez más, piezas de automóviles como núcleos de parachoques, parasoles, almohadillas de protección, cajas de herramientas (que se encuentran en la llanta de la rueda de repuesto y sujetan, por ejemplo, el enganche de remolque, el gato y las herramientas a bordo) o artículos de ocio.
La extrusión de espuma de espumas de partículas ofrece las siguientes ventajas sobre las espumas de partículas producidas en un autoclave :
- Producción económica, ya que se omite un paso del proceso (tratamiento en autoclave)
- Cambios de color más fáciles y rápidos
Las desventajas del material de extrusión, por otro lado, son una temperatura de procesamiento promedio más alta, combinada con un mayor consumo de energía y, en algunos casos, propiedades mecánicas significativamente más pobres en relación con la densidad en comparación con el material de autoclave.
Proceso de espuma de poliestireno
El poliestireno expandido (EPS) se produce mediante espumación física: el granulado que contiene el agente de expansión (5% de pentano ) primero se expande previamente a 40 a 80 veces su volumen calentando con vapor a aproximadamente 105 ° C y luego entre 3 y 48 horas a temperatura ambiente almacenado temporalmente para que luego el pentano pueda escapar hasta una proporción de aproximadamente el 3% y el aire pueda penetrar. Esto evita la creación de un vacío en el interior. En el caso de la formación de espuma terminada, el EPS preexpandido se llena en un molde y se expande calentándolo más a aproximadamente 130 ° C con vapor, es decir, llena el molde y las partículas individuales se funden juntas en los bordes. En el caso de moldes de bloques grandes, generalmente se aplica un vacío antes de que se introduzca el vapor de agua para promover la expansión de las partículas de EPS.
La densidad está determinada por el grado de preexpansión. Sin embargo, si es demasiado grande, el producto terminado colapsará.
Proceso de fundición de espuma termoplástica (TSG)
Al agregar agentes de expansión a una serie de termoplásticos , incluidos aquellos con cargas ( vidrio o fibras de carbono ), se pueden crear estructuras de espuma en las piezas moldeadas por inyección. Dependiendo del tipo y consistencia, los agentes de expansión se pueden mezclar en el granulado en un pequeño porcentaje o bombear a la masa fundida en el cilindro en un estado líquido a alta presión. En el núcleo, las piezas moldeadas resultantes tienen una estructura de espuma y una piel exterior muy compacta hacia la superficie. El método se utiliza para, por ejemplo, B. proporcionar piezas de paredes gruesas de piezas moldeadas por inyección con un núcleo de espuma para evitar marcas de hundimiento hasta la formación de espuma interna de piezas moldeadas de paredes relativamente gruesas para poder ahorrar peso sin tener que reducir el grosor de la pared. El método se utiliza para espesores de pared a partir de 2 mm, pero principalmente para espesores de pared entre 4 y 20 mm.
Las presiones necesarias para el proceso de inyección en la herramienta y la presión de sujeción son considerablemente más bajas que para el moldeo por inyección normal. Por lo general, las máquinas solo están equipadas con presiones de inyección de hasta aproximadamente 1000 bar. Los pesos de granalla se realizan a menudo con unidades de inyección de pistón que se llenan con un tornillo de preplastificación. Habitualmente se puede omitir una presión de retención, ya que la formación del contorno en la cavidad de la herramienta tiene lugar a través de la expansión del propulsor. Aparte de la última diferencia mencionada, el proceso es básicamente muy similar al moldeo por inyección normal. Se puede utilizar cualquier máquina de moldeo por inyección normal para el proceso.
El proceso TSG es adecuado para crear construcciones particularmente rígidas, ya que cualquier diferencia de espesor de pared se puede producir sin crear marcas de hundimiento. A menudo, varias herramientas se inyectan una tras otra en máquinas de mesa giratoria. Esto mejora el rendimiento a pesar de los largos tiempos de enfriamiento (debido a los grandes espesores de pared).
Espumas PUR
A diferencia del proceso de espuma de poliestireno, aquí el procesador utiliza materias primas líquidas y reactivas. Si se mezclan polioles con isocianatos y el propelente (generalmente agua), el poliol reacciona con el isocianato en una poliadición para formar PUR ( espuma de poliuretano ) y el propelente forma inclusiones de gas (con el agua propelente, este reacciona con parte del isocianato, liberando dióxido de carbono). Al poliol se le añaden aditivos como el agente de expansión, por lo que normalmente se utilizan dos componentes.
Las propiedades se pueden ajustar dependiendo de la selección de los materiales de partida. Así, cuando se utilizan polioles de cadena larga, se obtienen espumas blandas a elásticas, o cuando se utilizan polioles de cadena corta, se obtienen espumas duras fuertemente reticuladas.
El proceso principal es la espumación de cinta continua y los dos discontinuos RSG (moldeo por reacción de espuma) y RIM (moldeo por inyección de reacción) o procesos de baja y alta presión, siendo este último cada vez más generalizado.
En el caso de procesos discontinuos, se debe asegurar que se instalen líneas anulares para evitar que "sobresalgan" o se segreguen. B. el isocianato debe estar caliente por encima de los 15 ° C, de lo contrario cristalizará. También debe proporcionarse un sistema de limpieza para el cabezal mezclador para evitar que se pegue.
RRIM
Con RRIM (Moldeo por inyección de reacción reforzada), dos componentes ( poliol e isocianato ) y un material de refuerzo (por ejemplo , fibra de vidrio , fibra de carbono , polvo de roca) se mezclan en el llamado cabezal mezclador y se inyectan a alta presión en una herramienta de moldeo. Después de la reacción exotérmica de los componentes, se creó el poliuretano plástico termoendurecible y se puede quitar de la herramienta. Los ejemplos de aplicación son piezas de revestimiento exterior en la industria automotriz, como guardabarros, paneles de balancines y cubiertas de parachoques. Una ventaja del poliuretano sobre los termoplásticos es su relativamente alta resistencia al calor.
Proceso MuCell
En el proceso MuCell, se alimenta un gas inerte (nitrógeno o dióxido de carbono) a la masa fundida de polímero termoplástico y se mezcla en el cilindro de masa fundida para formar una solución monofásica. Cuando esta solución monofásica se inyecta en la cavidad de la herramienta de moldeo por inyección o soplado, o durante la extrusión cuando sale de la boquilla, la mezcla experimenta una caída de presión, lo que significa que el gas se nuclea sobre el componente y millones de células diminutas. crecer. Estas celdas luego reemplazan un volumen definido, lo que conduce a una reducción de densidad en el componente.
Desarrollos recientes
En los procesos de fabricación convencionales, las espumas se obtienen a menudo a partir de polímeros fundidos y agentes de expansión gaseosos. Una alternativa es utilizar plantillas microscópicas (las llamadas plantillas ) para darle a la espuma la estructura adecuada. Por ejemplo, se pueden distribuir finamente gotitas de agua en una solución de monómero y eliminarlas después de la polimerización. Otro método usa partículas para estabilizar las burbujas de aire en la mezcla de reacción. Un proceso recientemente desarrollado para la producción de poliestireno expandido se basa en la polimerización de emulsiones espumadas de aceite en agua . El estireno (fase oleosa) se emulsiona primero en una fase acuosa. Luego, la emulsión estabilizada por un tensioactivo aniónico se espuma con nitrógeno. Esto crea burbujas de espuma que están rodeadas por gotas de emulsión muy compactas. En el paso final, la polimerización se desencadena por exposición a la luz ultravioleta. Las gotitas de emulsión reaccionan mientras se retiene la estructura de la espuma. Las espumas poliméricas resultantes contienen poros que están parcialmente conectados entre sí. Esto permite el flujo de aire, fluidos u otros materiales a través de la espuma, lo que hace interesante la aplicación de materiales filtrantes o estructuras de marcos bioinspirados, por ejemplo.
Ejemplos de
- Espumas termoplásticas (por ejemplo, PS-E , PP-E y PVC-E )
- Espumas elastoméricas (p. Ej. , Espuma flexible PUR , NBR )
- Espumas duroplásticas (p. Ej., Espuma rígida PUR, PF )
Ver también
- Espuma floral
- Caucho celular
- Los agentes espumantes o agentes espumantes para la producción de espumas se describen en la Wikipedia en inglés en el artículo Agente espumador .
enlaces web
Evidencia individual
- ^ Foro de EPP en Bayreuth: Red de polipropileno expandido para EPP
- ↑ Fabian Schüler, Debora Schamel, Anniina Salonen, Wiebke Drenckhan , Michael D. Gilchrist, Cosima Stubenrauch: Síntesis de poliestireno macroporoso polimerizando emulsiones espumadas . En: Angewandte Chemie . cinta 124 , no. 9 , 2012, ISSN 1433-7851 , pág. 2256–2260 , doi : 10.1002 / anie.201107806 .